Phoenix 3D Printing is a revolutionary technology that allows you to create three-dimensional objects from a computerized design. It can also quickly prototype products and improve a business’s production processes’ efficiency.
First, the virtual design of an object must be made using CAD (computer-aided design) software. The resulting file must then be prepared for Printing using slicing software.
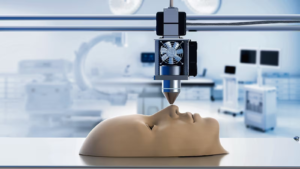
3D Printing, also known as additive manufacturing, transforms digital CAD models into three-dimensional physical solid objects. It is an alternative to traditional manufacturing methods like milling that rely on controlled material removal. 3D Printing can produce geometrically complex shapes and features that are difficult to achieve using other processes.
Technology is transforming many industries and revolutionizing how products are made, prototyped, and produced. It enables designers and engineers to develop ideas faster and bring new products to market more quickly, saving time and money. It can be used for functional prototyping, small/medium series production and end-use parts and assemblies.
As the use of 3D Printing grows, new materials and printer capabilities continue to be developed to expand the possibilities. Fused Filament Fabrication (FFF) 3D printing, the most popular technique in the industry, has seen major developments including advanced composites, fast print speeds and improved surface finish.
Composites with reinforcements like carbon fiber and glass are enabling stronger, lightweight components. Eco-friendly filaments made from recycled plastics or biodegradable materials are bringing added sustainability. Improvements in nozzle technology and motion control systems are producing finer details, smoother finishes and higher precision.
3D Printing is a powerful tool for education and can be used across many disciplines and subject areas to make learning fun, exciting and engaging. It has the potential to transform STEM subjects and help ignite students’ passion for design thinking, building their problem-solving skills, creativity and logical reasoning.
The applications of 3D Printing are endless – from medical and dental to aerospace and automotive to construction and education. It can create medical and dental models that help surgeons plan their operations before a patient’s procedure, produce customized prosthetics and orthopedic implants, and make architectural and construction models to streamline the design process.
With its ability to create geometrically complex shapes and textures, 3D Printing can also be used in the creation of decorative items. Wood and metal-infused filaments add a natural or luxurious touch to functional prototypes, while specialty filaments like conductive and magnetic materials enable the fabrication of electronic components and tools. Glow-in-the-dark and color-changing filaments are perfect for educational models and interactive art installations.
Fused Deposition Modeling
Fused deposition modeling, or FDM, is one of the most common types of 3D Printing. It uses a heated extrusion head to melt a filament of plastic that is then deposited layer by layer on the base of the print. The printed object can be constructed from any number of different thermoplastics, including rigid, translucent or elastomer plastics.
The first step of any 3D printing process is the creation of a digital design file. This can be done using a computer software program, which is usually free and widely available online. Once the design is ready, the digital file can be exported or downloaded to a printer, which will then produce a physical model of the design.
Once the printed object is complete, it can be sanded down, painted or bonded to other materials. 3D Printing is commonly used in industries such as automotive, aerospace, consumer goods and medical devices. This technology can also be utilized for prototyping or creating concept models of new products. Using this process, designers can quickly and easily create a prototype that can be tested and modified to improve performance or functionality.
While there are a wide variety of 3D printers on the market, FDM is a cost-effective option for companies looking to bring 3D printing in-house. When selecting a printer, it’s important to consider the company’s specific needs and use case. For example, what material properties are required? Will the prints be used for testing or validation purposes? What turnover times are needed? Selecting the right printer will ensure that the company has a reliable, high-quality printing solution that will fit in with the existing workflow.
Material Jetting
The material jetting (MJ) process resembles standard inkjet printer technology, where the liquid build materials are jetted onto the build platform in layers. Each layer is cured by UV light in the case of photopolymer materials or heat in the case of metal and ceramic materials. This printing process is commonly used for functional prototypes and is well-suited for parts that require smooth surface finishes and detailed aesthetics. However, it is less suited to producing final functional end-use parts that have demanding mechanical properties.
The MJ print process is relatively new and requires more complex equipment than other AM technologies, which can limit availability and impact cost. It also typically has slower print speeds than other AM technologies, which can affect large-scale production and rapid prototyping. It also requires extensive post-processing, such as sintering and curing, which can increase the time and cost of a printed part.
Unlike FDM and SLS, which print parts one-layer-at-a-time, MJ printing produces the entire 3D part in a single pass. This allows for higher resolution and enables the use of multiple materials and colors in a single build. This multi-material and color capability makes the MJ print process ideal for over-moulded parts, and enables the creation of highly accurate visual and haptic prototypes. MJ is also capable of printing rubber and rigid materials, which can be blended to create complex and unique material properties. When designing for MJ, it is important to keep in mind the varying characteristics of each material, and to consider how they will interact with each other during the printing process. In particular, it is important to consider the interaction between the liquid droplets and each previous printed layer (the wetting condition), as this will significantly influence the quality of a print. This includes issues such as shrinkage, layer height variations, oxygen inhibition, and the coffee-ring effect. These effects can be minimized by careful design and proper curing of the printed parts.
Rapid Prototyping
As the name suggests, rapid prototyping is a type of prototyping process that is used to rapidly fabricate physical prototypes using three-dimensional computer-aided design data. This is in contrast to more traditional manufacturing processes like subtractive machining, where a block of material is cut away from the object, or compressive methods like casting, forging and molding, where a semi-solid or liquid material is forced into the desired shape before solidification.
The prototyping process helps to ensure that all the design, mechanical, electrical, and thermal components of a product work together and fit properly, without incurring any costly errors that might occur during production. Typically, engineering teams will create low-fidelity prototypes of critical subsystems and systems to test and iterate on them at the same time as they are integrating the individual parts into an overall working model. This enables them to identify potential issues and resolve them before they can affect the whole system, which will then be easier to verify once all components are working together as a unit.
Engineers can then use these functional prototypes to gain customer and client feedback on their products, and to communicate their intended production specifications to tooling specialists for final fabrication. This allows them to avoid expensive product re-designs and manufacturing issues later down the line, as well as to streamline workflows with jigs and fixtures that can be printed directly on the production line.
Prototypes also empower designers to present their ideas to clients and investors with clear, actionable user feedback in ways that can be difficult or impossible to convey on screen. This visualisation can also help to speed up the approval process and improve communication between different departments, ensuring that everyone has a shared understanding of what is being developed and how it will work in practice.
With so many advantages, it is no surprise that the use of 3D Printing in the design and manufacture of consumer electronics and medical devices is growing. This technology offers a faster, more cost-effective and accurate way of producing high-quality prototypes for all types of applications.